Blog
14/07/2023
The rise of the intelligent manufacturing metaverse: Unveiling the power of digital twins and digital threads
Digital twins and digital threads enable companies to innovate faster, optimize resource usage, and identify bottlenecks early on. Manufacturers can leverage these technologies to operate more efficiently and achieve their sustainability goals.
Digital transformation (DX) is a top priority for enterprises worldwide, shaping entire industries. Financial analysts estimate that global DX spending will reach $3.4 trillion by 2026, which is more than double compared to 2021. Approximately one-third of this will go toward augmented maintenance and other manufacturing processes. We’re also witnessing the rise of digital twins and digital threads, two technologies that drive efficiency, sustainability, and innovation.
But what is this change in practice, and how should the manufacturing industry react to it?
Digital twins are virtual replicas of physical objects or systems that use real-time data and simulations to enable analysis, monitoring, and control. A digital thread, on the other hand, is a seamless flow of data that connects the entire lifecycle of a product, from design to manufacturing, maintenance, and beyond. These technologies can be used together to improve production processes and product quality.
Manufacturing companies leverage digital twins and threads to test different scenarios, speed up innovation, and maximise resource usage. These practices can result in lower costs and contribute to a more sustainable future, among other benefits.
How digital twins are shaping the manufacturing industry
Product development can be expensive and resource-intensive and often involves a lot of trial and error. One way to save resources and cut costs is to digitise the product lifecycle by creating virtual replicas of a particular item or system.
For example, a car manufacturer may create a digital “twin” of a physical vehicle, including its design, mechanical hardware, software controls, etc. This would allow the company to run endless simulations, identify and address potential errors, and improve its operations. The simulation can take place in real-time or faster than a real-time simulation, enabling insight into what could happen in the future with the testing results.
Enterprises can also use digital twins to make better decisions based on real-time insights. Moreover, this technology can minimise the delays in product development, resulting in a shorter time-to-market and lower costs. Other potential benefits include:
- Improved resource allocation
- Reduced energy consumption
- Shorter learning curve
- Increased productivity and efficiency
- Improved worker safety
- Optimised supply chains
- Higher product quality
- Less downtime
- Higher profits
The role of digital twins becomes more important in a world where sustainability has taken centre stage. This technology aligns with the European Union’s commitment to achieving net-zero greenhouse gas (GHG) emissions, allowing companies to reduce waste.
For instance, manufacturers can use digital twins for predictive maintenance. By analysing data from sensors and other sources, they can predict potential failures or inefficiencies, which may help reduce downtime and optimise resource usage.
Samsung, Boeing, Bridgestone, Electrolux, Kaeser, and other industry giants use digital twins for product development and maintenance.
Boeing, for example, leverages digital twins to create new parts and systems for its aircraft, prevent unscheduled maintenance, and address inefficiencies. The company also uses digital threads based on data to expand upon these digital twins.
Similarly, Electrolux plans to create digital twins in its factories. The Swedish manufacturer uses this technology to run simulations, optimise assembly processes, test new concepts, and reduce manual work.
Digital threads connect the virtual and physical worlds
In the manufacturing industry, digital twins and digital threads are often used together to optimise production processes and improve product quality.
For example, a digital twin of a machine or production line can be used to simulate different scenarios and identify areas for improvement. The data generated by the digital twin can be fed into the digital thread, providing real-time insights that help optimise production schedules, reduce downtime, and increase efficiency.
Digital threads are streams of data collected throughout the product lifecycle. These include the design, testing, simulation, performance data associated with digital twins, and other critical information, such as production and supply chain data.
Companies can analyse these data sets to measure the performance of their products, operations, or systems. Therefore, digital threads may help prevent common issues in the manufacturing process, including but not limited to technical bugs, product recalls, and budget overruns.
This technology can also streamline collaboration and data sharing across design teams, enabling concurrent engineering. As a result, it may increase design efficiency and reduce material waste. At the same time, it allows manufacturers to incorporate sustainable design principles early in the product development process.
Another advantage of digital threads is their ability to track and trace materials throughout the supply chain. This practice ensures transparency and compliance with sustainable sourcing practices, helping companies reduce the use of hazardous materials.
But that’s not all. Digital threads also enable real-time monitoring of manufacturing processes, collecting data on energy consumption, emissions, and quality. Manufacturers can act upon these insights to optimise production parameters and resource usage.
Digital twins and digital threads could pave the way to a greener future
Some of the world’s biggest companies use digital twins and digital threads to drive innovation. These technologies offer a plethora of benefits, from higher efficiency and lower costs to improved collaboration. They also allow manufacturers to understand their data better and make more informed decisions.
From an environmental standpoint, digital twins and threads can help companies become greener and achieve sustainability goals. These practices enable enterprises to digitise their workflows and shift to new, low-impact business models.
For example, companies may use digital twins to assess the impact of alternative energy sources on their operations. This approach would allow them to test different scenarios so they could choose the most sustainable and cost-effective solution.
Digital twins and digital threads work together seamlessly, connecting the virtual and physical worlds. The sooner you embrace these changes, the better you’ll be able to tap into their full potential and make your business greener.
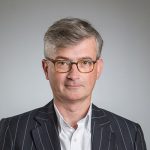
Ilkka Donoghue
Manufacturing Practice Lead
Read next
07/08/2023